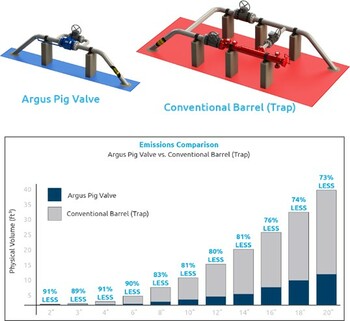
Nicolaas Ainsworth discusses advances in equipment used to introduce and remove gear from pipelines.
Pipelines are essential to our modern energy infrastructure as one of the safest, most economical, and environmentally friendly means of transporting fluids today.1 But the infrastructure that stands as a cornerstone to our way of life is not invulnerable. Without proper corrosion and material build-up maintenance, leaks, blockages, and complete operation shutdowns can happen.2,3 The resulting consequences are inefficient flowrates, profit loss, environmental damages, infrastructure death, regulatory compromise, safety risks, and heightened dangers of fires and explosions.1,2,3 Midstream operators commonly introduce pipeline pigging into their maintenance programmes to avoid these risks and ensure a healthy line.
By sending ‘pigs’, through a line section, operators can purge the line of harmful materials that would corrode or build up and block the line if left unchecked.2,3 Additionally, by sending inline inspection tools or ‘smart’ pigs through a line, operators can survey the state of their infrastructure and be proactive in facilitating its integrity.4 The advancements in pigs and the continuously improving support to line integrity are stupendous and much acclaimed. Less talked about, though, is the advances in the equipment we use to introduce and remove the gear from our pipelines.
Pig Barrel Trap: The Traditional Method
The benefits that sending a pig through a pipeline has on its integrity may be apparent; however, introducing and removing that pig from a pipeline can be less intuitive. Pigging requires implementing pig launching and receiving stations on opposing ends of a line segment. At the launching station, the operator inserts the pig into the station and sends it through the line to be captured and removed at the receiver station. Traditionally, these stations use a complex barrel set-up with multiple isolation, drain and kick valves to complete the process. This type of station is known as a pig barrel trap or pig barrel station. While barrel traps will allow you to pig a pipeline, the system has many severe limitations and risks, reducing its effectiveness at improving infrastructure integrity.
The innate design of the pig barrel trap requires the infrastructure to take up a significant amount of space. The footprint and weight of the barrel trap can make introducing the station challenging, if not possible or practical, for many lines. Numerous pipelines can become considered ‘unpiggable’ simply because the barrel traps cannot be introduced, and the operator may be unaware of the alternative.4 The inability to run pigging operations on these pipelines compromises the integrity of the infrastructure, leaving midstream operators with few choices.
The design of a barrel trap additionally poses an increased risk to the operator’s safety. Due to the horizontal alignment of the barrel, operators may be at risk of being struck by pigs propelled at high speeds from the gas pressurisation in the line if a mistake is made during the procedure.5,6 When these mistakes happen, the force and forward-facing direction the equipment launches can lead to severe injury or death if struck. Unfortunately, the occurrence of these incidents and their corresponding consequences are well documented.7 The complexity of the pig barrel trap only adds to the danger. The complexity of the station requires numerous complex systematic steps to operate safely, providing more opportunities for human error.8 These innate design features explain why pigging is considered a significantly dangerous operation.
Pig Valves: Modern Method to Pigging Stations
Higher standards for environmental friendliness and operational safety, increased offshore operations, and the increasing desire for maintenance on more lines exasperate pig barrel traps’ issues and limitations. Pipeline operators need a better alternative to launch, receive and maintain pigs. Fortunately, technology has grown, and there is a better choice. A modern solution to the traditional pig barrel stations is an alternative trap structure known as a pig or scraper valve. The concept of a pig valve is to use a trunnion-mounted, quarter-turn valve with an entry point to allow the sending and receiving of pigs. The design, typically accompanied by piping bypass and block valves, enables operators to achieve double block and bleed positive shut-off upstream and downstream while sending or receiving a pig.9 The design of the pig valve overcomes the pig barrel trap’s safety, operational complexity, and size issues with the added benefits of higher environmental friendliness and more straightforward maintenance.
The Argus pig valve is one of the best examples of a pig valve or scraper. Argus is renowned globally for its innovative pigging stations, especially its pig valve. Its design eliminates the projectile risk operators face when pigging with a barrel. The Argus pig valve uses top-entry loading mechanisms that keep operators out of harm’s way when loading or removing.9 If a mistake does occur in depressurisation, the pig will not launch toward the operator as it is not horizontally facing. However, that risk is more or less moot, as the valve design makes it nearly impossible to actually open with pressurisation, as by the time the cap is fully open, and the pig exposed, all pressure would have likely escaped. Furthermore, pig valves have substantially smaller configurations with much fewer valves and infrastructural components than barrel traps.9 Thanks to its simplification, pig valves often require fewer steps, reducing the opportunity for human failure and any of this occurring.
In addition to removing operational safety risks, the pig valve also extends the number of pipelines that can undergo pigging operations. The pig valve has a much smaller footprint than a traditional barrel trap and is far lighter.9 The compact size of the valve station infrastructure makes pigging possible in previously impossible areas and more practical in others. The lighter weight of the pig valve station infrastructure also makes it more suitable to use where this is a significant concern, such as on offshore platforms. By providing more opportunities to implement pigging operations, the pig valve enables operators to elevate the efficiency of the flow rates of their pipelines and reduce the need for costly replacements, leading to higher revenue generation.
As noted, in addition to overcoming the issues of the barrel system, the pig valve has the benefit of reducing maintenance difficulties and significantly lowering GHG emissions.9 The simplification of its configuration means fewer components need upkeep, and there are fewer points for potential failure, improving maintenance. The pig valve also requires much less physical volume to vent than a barrel. The Argus pig valve, for example, reduces the amount of emissions by up to 91% compared to a barrel trap.9 The drop in emissions makes the pig valve ideal for companies searching for ways to help decarbonise their operation.
Automated and MPL Valves: Further Optimisation of Pigging Stations
The pig valve is not the only advancement in pigging stations. An issue plaguing many operators is what to do if their pipeline needs frequent purging of corrosive or damaging residues. The problem is quite common in wet gas pipelines. Pipelines carrying wet natural gas, sour gas, and others are susceptible to the gas slowing down and liquifying in areas through a phenomenon known as liquid loading.3 The puddles of the liquified gas sit and slowly eat away at the walls, creating leaks and cracks. In addition, the puddles can block gas from running through the line, leading to profit loss.3
Pipeline pigging is the only realistic solution to mitigate the pooling. However, the pigging frequency necessary to make it effective can be problematic. Sometimes, operators must purge their line through pigging operations multiple times a day to stay ahead of the problem. Operating a barrel trap station numerous times a day is time-consuming and expensive. A pig valve is a better solution but still has limitations in needing to be reloaded per operation. An alternative innovation to pigging stations built to overcome this problem is automated pig launchers such as the Argus Multi-Pig Launcher (MPL). The Argus MPL takes a pig valve and applies a vertical barrel to the top entry. (There are alternative automated launchers that use horizontal barrels, but these stations fight gravity and can be prone to failure.)
The operator can preload their station with several pigs using a vertical barrel. Preloading the pigs allows operators to consolidate up to eleven operations (in the instance of the Argus MPL) into one. The operator can manually send the pigs through the line, but the station usually has an actuator allowing remote launching. The clear benefit of having the actuator is midstream and upstream owners need to send only one team every eleven launches to load the MPL. Consolidating the operations cuts travel and operation costs while removing safety risks and emissions associated with travel. These benefits also make the station ideal for pigging in locations that are difficult, or periodically impossible, to reach.
Conclusion
Pipeline pigging is vital to ensure the integrity and longevity of pipeline infrastructure by allowing operators to remove build-up that reduces flow efficiency while purging the line of harmful debris that can cause corrosion and rust, leading to leaks and failures.1,2,3 Pigging is also crucial in enabling operators to inspect their infrastructure and be pre-emptive in mitigating failures.4 The incredible advancements in pipeline maintenance and ILI pigs have been a hot industry topic; interestingly, the advances in the stations necessary to use the gear are less spoken about. There appears to be some misconception of what modern alternatives to the traditional pig barrel trap or station are available. As many of the pain points of running pigging operations stem from the stations you use to pig, it is interesting why the alternatives are less spoken about.
Entering a pipeline with a pig has traditionally been a complex, costly, and often dangerous activity due to the innate design features of the pig barrel traps or stations necessary to introduce and remove pigs from the line.5,6 Innovations in the system for launching and receiving pigs are helping solve the issues of the traditional stations while providing additional benefits to GHG emission reduction and more. Pig valves such as the Argus pig valve eliminate the safety risks associated with the conventional barrel trap using a vertical loading mechanism and an entry cap.9 Additionally, the compact size and smaller infrastructure footprint extend the number of pipelines operators can maintain by pigging. Innovations in automated pigging stations like the Argus Multi-Pig Launcher also support operators who require high-frequency pigging or pigging in remote areas by consolidating operations and utilising actuation technology. Both these systems also massively reduce GHG emissions and operational complexity. In summary, the innovations in pigging stations are helping pipeline operators increase revenue, save infrastructure, reduce GHG emissions and extend operator safety.
References
1. PHMSA, “PHMSA and Pipelines FAQs,” 8 May 2017. [Online]. Available: https://www.
phmsa.dot.gov/faqs/phmsa-and-pipelines-faqs
2. WEIDONG, L., QIYU, H., WENDA, W. and XUEDONG, G. , “Advances and Future
Challenges of Wax Removal in Pipeline Pigging Operations on Crude Oil Transportation
systems,” Energy Challenges, 2020.
3. DALL’ACQUA, D., BENUCCI, M., CORVARO, F., LEPORINI, M., COCCI GRIFONI, R., DEL
MONACO, A., DI LULLO, A., PASSUCCI, C. and MARCHETTI, B., “Experimental results
of pipeline dewatering through surfactant injection,” Journal of Petroleum Science and
Engineering, pp. 542 - 552, 2017.
4. CLARK, T. and NESTLEROTH, B., “Gas Pipeline Piggability,” Battelle, Columbus, 2004.
5. National Energy Board, “Pipeline Pigging Operations: Open to Injury,” National Energy
Board, Calgary, 2007.
6. MCKNIGHT, N., POE, R. and HARRISON, P., “Keeping Safety Grounded in Hydrogen
Takeoff: Revisiting Risk in Pig Launching and Recieving,” Pipeline Technology
Conference, 2022.
7. Occupational Safety and Health Administration, “Accident Report,” 25 June 2012.
[Online]. Available: https://www.osha.gov/ords/imis/accidentsearch.accident_
detail?id=33816.015
8. DRINKWATER Products, “Pig Launching and Receiving Procedures,” Drinkwater Products
LLC, 2014. [Online]. Available: https://www.drinkwaterproducts.com/pipeline-piggingresources/
pig-launching-and-receiving-procedures. [Accessed 2023]
9. Argus, “Pigging Valves,” 2022. [Online]. Available: https://www.argusinnovates.com/
products/view-product/pigging-valves
Leave A Comment